Category: เครื่องแยกและผลิตก๊าซ CO2 & CO2 Recovery Plant > Acid Gas Removal > |
Acid Gas Removal 
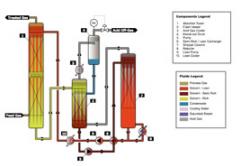
Overview
The Wittemann Company LLC -- Industrial Division designs and manufactures Acid Gas Removal Systems for numerous applications. A Stack Gas CO2 Recovery System, as designed and manufactured by Wittemann, is also an Acid Gas Removal System. We distinguish this system because of the distinct source and nature of that application. Typically, a stack gas system employs a patented solvent to recover CO2 from exhaust streams emanating from a boiler, an engine, a turbine, etc. The common characteristic is that the exhaust has from one to fifteen percent (1%-15%) oxygen in the exhaust stream.
Acid Gas Systems, as typically understood, do not have oxygen in the process stream. The solvent employed to remove CO2 and sulfur from the process gas is not oxygen tolerant (protected). Additionally, the process stream is at a higher pressure, which embraces the ability of solvents to remove CO2 and sulfur compounds.
Gas treating is the absorption of acid gases such as carbon dioxide and hydrogen sulfide from natural gas, synthesis gas, refinery tail gas, and flue gas.
Process selection depends on the raw gas conditions and treated gas specification. The most important raw gas condition is the acid gas partial pressure (mole fraction of acid gas times the total pressure, usually expressed in mm Hg). The chemical solvents of choice are alkanolamines. Alkanolamines are weak basic compounds that react with certain acid gases, forming weak chemical bonds. These bonds are easily broken upon mild heating. The strength of the alkanolamine's bond and the corresponding heat needed to break it depends on the number of organic hydrocarbon groups attached to the nitrogen atom. Depending on the number of such groups, alkanolamines are classified as either primary, secondary, or tertiary. Alkanolamines are used primarily to absorb carbon dioxide and hydrogen sulfide. Carbon monoxide and nitrous oxides are very weak and do not chemically react with alkanolamines.
Sulfur dioxide and nitrogen dioxide form very strong chemical bonds with alkanolamines. The heat required to break these bonds would decompose the alkanolamines themselves. They must be removed before treatment. Carbonyl sulfide and carbon disulfide react with primary amines, forming non-regenerative decomposition products, except in the case of diglycolamine (DGA). Carbonyl sulfide and carbon disulfide do react with secondary amines, forming regenerable compounds, but they are not appreciably reactive with other amines. Mercaptans are such weak acid gases that they are not readily removed by any of the alkanolamines. Mercaptans are often removed by treatment with caustic.
Monoethanolamine (MEA) and diethanolamine (DEA) became the dominant commercial absorbents. Companies such as the Girdler Corporation developed monoethanolamine chemistry into a commercial process. Other amines were developed as a result of specific industry needs. Disopropanolamine (DIPA) found commercial application in Shell's Sulfinol process, where it is mixed with Sulfolane (tetrahydrothiophene dioxide) and water. DIPA based processes are used primarily to treat refinery gases because of their ability to treat gases containing carbonyl sulfide, carbon disulfide and certain mercaptans. Diglycolamine (DGA) has a lower vapor pressure and lower inherent corrosivity than MEA. It was developed primarily as a substitute for MEA. Methyldiethanolamine (MDEA) has been technically available since 1950, but has only recently become commercially popular. MDEA combines the low regenerative heat requirements of a physical solvent with the ability to selectively remove hydrogen sulfide from a gas stream containing both hydrogen sulfide and carbon dioxide.
Primary Amines
MEA and DGA are primary amines. MEA with one ethanol group attached to the basic nitrogen atom is the strongest amine. It reacts quickly with both hydrogen sulfide and carbon dioxide, forming strong but thermally regenerative chemical bonds. MEA is effective at removing virtually all hydrogen sulfide and carbon dioxide, but requires a large quantity of heat to regenerate, i.e.: break the chemical bonds formed. MEA is used when the specification requires maximum hydrogen sulfide and carbon dioxide removal, particularly at low pressure. MEA reacts with carbonyl sulfide and carbon disulfide, forming non-regenerative degradation products.DGA [2-(2-aminoethoxy) ethanol] was jointly developed by Fluor, El Paso Natural Gas, and Jefferson Chemical Company. DGA is similar in performance to MEA, but DGA has a lower vapor pressure, which results in less solvent vaporization losses. DGA forms regenerable reaction products with carbonyl sulfide and carbon disulfide. Typically, this regeneration is carried out in the reclaimer at elevated temperatures, as opposed to the reboiler where carbon dioxide and hydrogen sulfide are removed. DGA was specifically developed to replace MEA in low-pressure applications as a means of reducing vaporization losses.SECONDARY AMINES
DEA and DIPA are secondary amines with two ethanol groups or two isopropanol groups, respectively, attached to the nitrogen atom. The additional alcohol groups draw more of the free electron character away from the nitrogen atom, which makes secondary amines somewhat weaker bases. Secondary amines are suited for gas steams with less stringent product specifications. DEA is used when the specification allows for some carbon dioxide to be left in the treated gas. DEA does not form non-regenerative degradation products with carbonyl sulfide, which makes it a suitable choice for treating refinery gases. DIPA is used almost exclusively in refinery operations to remove carbonyl sulfide and hydrogen sulfide. DIPA is used with additives in both the Adip process and Sulfinol process. Secondary amines are less corrosive, require less heat to regenerate and can be used in treat gas streams containing carbonyl sulfide and carbon disulfide. However, secondary amines are not effective at deep carbon dioxide removal.
Tertiary Amines
MDEA and TEA are tertiary amines. MDEA has two ethanol groups attached to the nitrogen atom, along with a methyl group. MDEA is a weak base that reacts much faster with hydrogen sulfide than with carbon dioxide, making it particularly selective under the proper design conditions. MDEA is used selectively on higher-pressure gas steams (20.6 Bar G. and above) for deep hydrogen sulfide removal with only moderate carbon dioxide removal. MDEA can also be used non-selectively for bulk removal of carbon dioxide from gas streams, but bulk removal requires the aid of absorption enhancing additives. TEA is also a tertiary amine. TEA has three ethanol groups attached to the nitrogen atom. It is the weakest amine and requires the least heat to regenerate. TEA is used only on high-pressure gas streams when even moderate acid gas removal is not essential. Tertiary amines are less inherently corrosive and can be used in higher concentrations, but tertiary amines are not a good choice when the raw gas pressure is low or the specification calls for deep carbon dioxide removal. However, tertiary amines, particularly MDEA, are well suited for selective absorption on high-pressure gas streams.
Formulated Solvents
Formulated solvents are proprietary mixtures of traditional amines, antifoamers or corrosion inhibitors. Most formulations are based on tertiary amines (MDEA, TEA or "statically hindered" amines) and are designed to be used selectively. Formulated solvents are promoted as high performance solutions and command a higher price. It is difficult to determine the applicability of formulated products without relying heavily on the projections or past experience with the same formulation. The cost of the formulation must be evaluated against the level of performance.
Gas Plant Operations
There are a number of treating problems that are associated with almost every gas plant sometime in its operating lifetime. The four most common treating problems are corrosion, foaming, chemical losses, and degradation. Some of these problems affect the quality and performance of the treating solution; others add to maintenance and operating costs.
The Wittemann Company LLC -- Industrial Division designs and manufactures your system after careful analysis to determine:
The most cost effective solvent
Elimination (curtailing of):
- Corrosion
- Chemical losses
- Foaming
- Solvent degradation
This provides the industrial gas supplier with a first-in cost balanced by a life cycle cost, enhancing ROI.